
Workshop participants must be at least 18 years. Turn around time for glaze firing can vary depending on how busy the kilns get but your cup will be available for pick-up within 4 weeks.Īll workshops are private lessons with ceramic artist and UW Art faculty, Timea Tihanyi. (Please also add “Additional Glazing and High-Firing” to your cart before checking out. Standard glazing and high-firing are an additional fee ($20-50), depending on number, size and complexity. Select number of successful pieces are bisque fired and can be picked up in 2weeks. Advanced printer operation and maintenance basics. Trimming, finishing and getting your work ready for firing. Ceramic hand-building with 3D printed components. Printer set-up and printer operation basics.Īmple printing and experimentation time. Slicing and trouble-shooting an STL file for printing.Ĭlay preparation. Intro to the Rhino design environment, nuts and bolts of making solid models for 3D printing.įorm development and structural issues for printable ceramic designs. During the academic year we don’t list regularly scheduled dates. Please email to confirm date and start time before registering. Personalized instruction at Beginner and Intermediate levels.
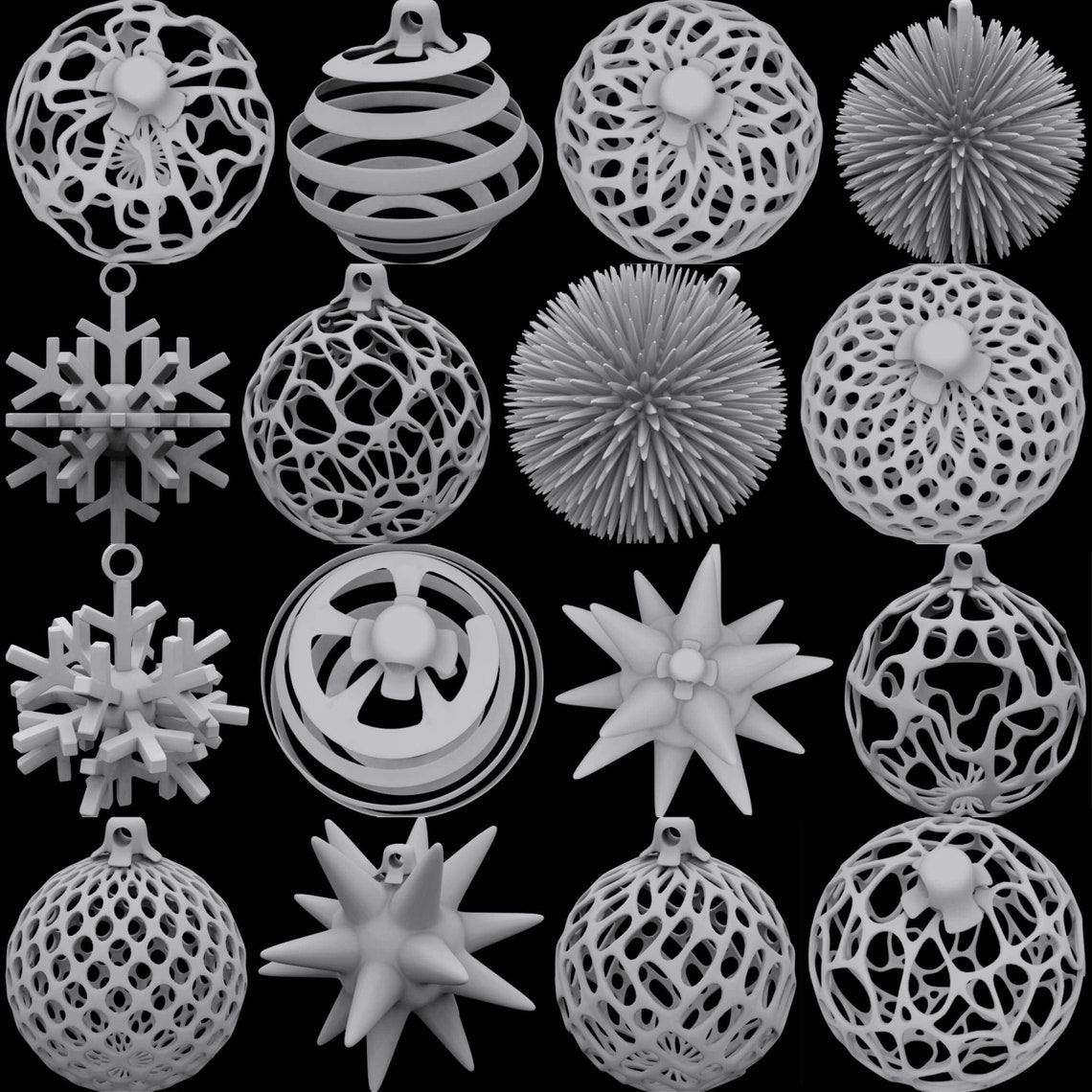
Of course none of this will work if you have to generate your printer’s motion commands yourself or by some other way.One-day (4.5 hours) on Saturday, and two-day workshops (9 hours) on both Saturday and Sunday. Make a Loft from #4, export that as an STL file, and run it through a slicer specifying Vase Mode and a layer height defined as above.Scale CI & C2 to the various diameters your final shape requires, then move each pair to the appropriate height.Move C2 up by the thickness of your printed layer.Make C2 by rotating it’s peaks to coincide with the valleys of C1.

divide each by the number of wiggles per loop, make an Interpolated curve C1 by using alternate points from each circle.) (Circle 1, Circle 2 offset from Circle 1 by the distance of a wiggle.

What is the source for your toolpath definition? Non-clay FDM printers generate the end effector tool path by using a slicing program that reads in an STL file definition of the part to be printed and outputs the GCode commands required to print it.
